Main navigation
Recycling of the future – marked plastic as a circular product
Plastics are harmful to the climate and human health both during manufacture and combustion and they also clutter our planet with garbage. Recycling is therefore a key issue, but at the moment it is not efficient. Polysecure has developed a process for permanently marking individual plastics that enables them to be separated efficiently and returned to a circular economy. This would counteract the vast amount of (micro) plastics and reduce CO₂ emissions.
Putting liquid detergent in the washing machine, removing cereal from foil packaging, brushing our teeth, taking a coffee to go to a meeting where you sit on a polyester chair. Plastic has become an integral part of our everyday lives. The huge variety of plastic products is mainly produced from oil and gas, with the addition of substances such as softeners, barrier additives and similar. Every year, Germany produces more than 3 million tonnes of plastic packaging waste1. Even though plastic garbage is collected in yellow bags, only a very small proportion of it is recycled. Most garbage is either burned or shipped to other countries. New plastic packaging material currently consists of no more than 15% recycled plastic. So where does the problem lie?
Plastics must be single-variety to be used for producing recycled packaging material
In Germany as in the rest of Europe, packaging is subject to what is known as extended product responsibility: everyone who places packaged goods on the market is responsible for ensuring that the packaging pollutes the environment as little as possible. This is made difficult by changes in society that increase plastic consumption, with trends such as eating on the go, a convenience lifestyle and online offers. Perishable goods are also specifically or individually packaged to make them last longer. High-quality recycling of packaging is therefore particularly important.
"Recyclable plastic materials must be single-variety or single-origin and best of all, should adhere to particular specifications so that they can be reused in packaging that is part of a circular economy,” explains Jochen Moesslein, founder and managing director of Polysecure, a technology company in Freiburg. Conventional sorting systems are only able to differentiate between the main polymers such as PET (polyethylene terephthalate), PE (polyethylene) and PP (polypropylene). “It is not possible to differentiate between subclasses or specifications. Furthermore, multilayer films that are key to increasing the shelf life of food cannot be identified. They all end up in the mono flows where they interfere with single-variety processing. It is not yet possible to find out whether packaging was intended for food or non-food applications."
The shortcomings of conventional sorting systems are one reason why only around 15 percent of the 5.2 million tonnes of plastic waste generated in Germany in 2017 were recycled1. This is why the German government’s Packaging Act aims at increasing the plastic packaging recycling rate to 62 percent by 20222. Moesslein`s objective is to improve plastic sorting by efficiently separating materials with similar physical properties. He comments: "We are looking to create a circular economy in which waste plastics are separated according to application-specific groups and/or brands so that they can meet certain specifications and be used again." This would also involve the removal of certain contaminants, e.g. separating non-food packaging from food packaging. All of this becomes possible with the tracer-based sorting (TBS) technology developed by Polysecure.
Unique marking technology
The technology’s core idea is to mark processed plastics with fluorescent particles: “The tracers are differentiated by their fluorescence. In this way, every plastic or element of packaging can be identified according to its specification,” says Moesslein, a physicist and business economist who employs 13 people in his Breisgau-based company. For this purpose, the tracers are mixed into the plastics or - especially in the case of packaging - applied to the surface via printing while still in production. The fluorescence ensures that the marked materials can be detected in the waste flow, sorted and removed along with the fluorescent tracer and printing inks, and subsequently be re-used. A tiny tracer amount of 100 micrograms per packaging is sufficient. This keeps tracer costs low in relation to the value of the plastics. The tracer materials need to be inert, insoluble, mechanically robust and thermally stable across a wide range of temperatures. This means that the plastics only have to be marked once and can still be used during several extrusions and processing steps. Moreover, another crucial aspect is biocompatibility, to avoid any danger if marked packaging accidentally ends up in the environment.
In addition to sorting plastic materials, Polysecure’s tracer technology can also be used for product authentication and protection against plagiarism. "Using our tracer technology, original manufacturers can protect themselves against unauthorised warranty claims and product piracy," explains Moesslein, explaining the original idea behind the founding of the company in 2009. Individual objects can even be traced using random particle patterns that the tracers create in the materials. With this in mind, the Polysecure team, in cooperation with partners, is currently developing a solution for counterfeit-proof product tracking of medical test systems with partners.
Comprehensive value chain - nationally and globally
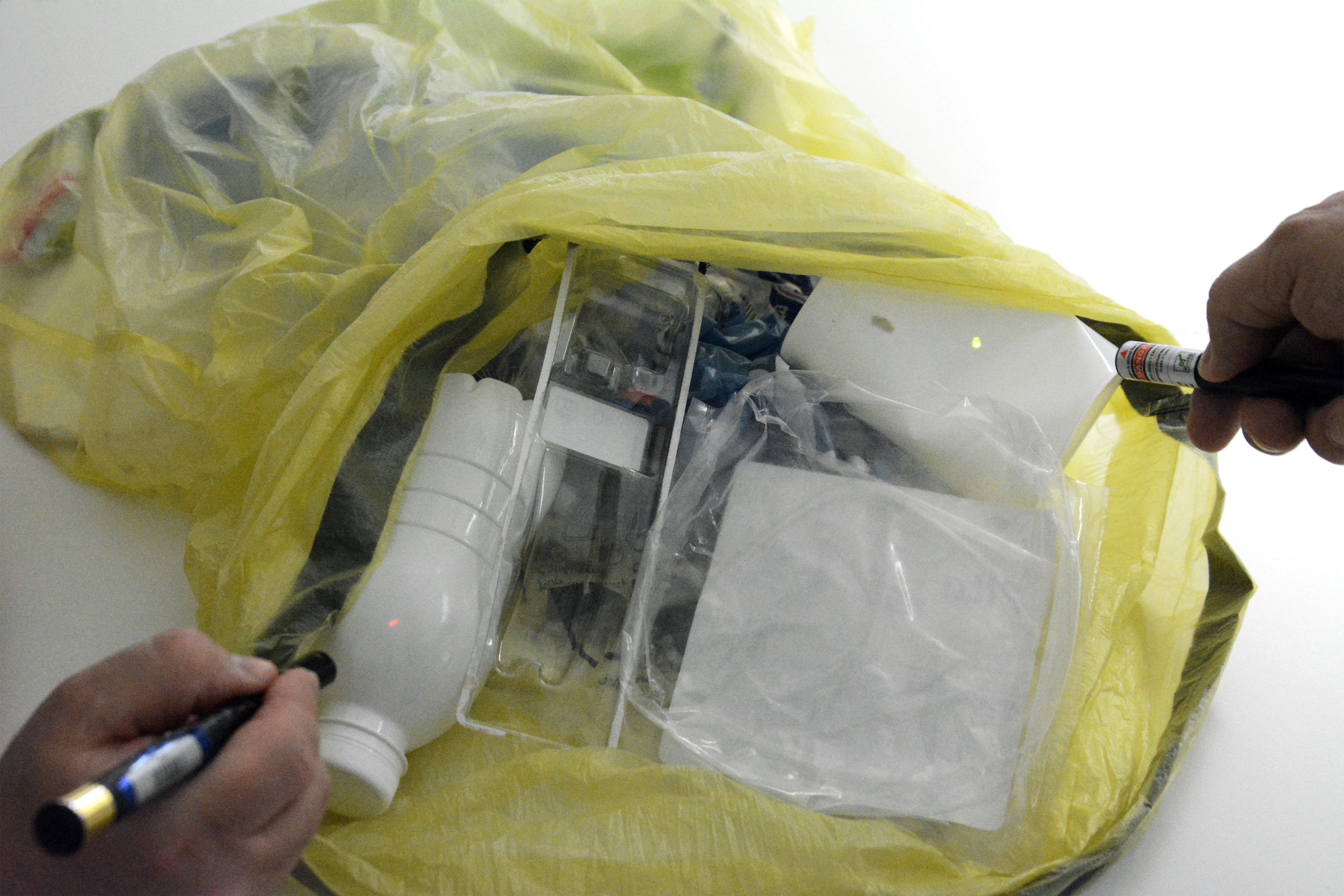
Around 40% of all plastic waste worldwide stems from plastic packaging. Approximately 150 million tonnes are thrown away every year. The objective is to use plastic materials to produce new, high-quality materials that will reduce CO2 emissions. However, the high-quality recycling of plastics requires much more effective sorting systems than those currently available. According to Polysecure, the percentage of recycled plastics can probably be increased to 70%, possibly even 80% using TBS and another approach known as design for recycling that helps design more environmentally friendly products.
On a global scale, this would help replace up to 60 million tonnes of plastic that would otherwise have to be produced from oil or gas. Moreover, it would also contribute to reducing over 100 tonnes of CO2 emissions. “The sustainability aspect is hugely important for us,” says Moesslein, going on to mention another factor that underlines the importance of recycling plastics: “As far as implementing sustainable innovation is concerned, it is also important that TBS not only significantly improves the recycling of plastic packaging, but also makes it cheaper. Only once recyclates are able to compete with new plastics, will they no longer end up in the countryside and in landfills.”
Polysecure is working with partners such as the Karlsruhe Institute of Technology (KIT) on further developing the tracers. The company is currently working on a project called MaReK (tracer-based sorting and recycling system for plastic packaging) funded by the BMBF in cooperation with Grüner Punkt, Werner & Mertz and Pforzheim University of Applied Sciences. Polysecure developed the first industrial TBS sorting machine for a company called REHAU. It can be used to separate PVC that contains glass fibre and pure PVC from co-extruded window profiles.
The MaReK partners and Polysecure have started an international stakeholder process to implement the new tracer technology. "Initially, it was all about making the new process known," reports Moesslein. “Now, more concrete talks with brands, packaging manufacturers, disposal companies and politicians are taking place. On the technical side, specific applications are being tested and corresponding business models calculated. It is a very exciting time. The systems could feasibly be implemented relatively quickly in less developed countries where there is currently little or no sorting technology and which might be interested in installing a new sorting technology such as TBS. This “leapfrogging”, i.e. the skipping of certain stages in the technological evolution, is also known from other applications such as renewable energies."
The Freiburg-based company is particularly interested in exchanging information and experiences with stakeholders, industrial partners, investors and politicians. The aim is to achieve a meaningful transformation into a sustainable economy by implementing the TBS process. What was once a wonder of alchemy developed through a combination of petroleum and human know-how, can only be separated efficiently by further, more advanced know-how. Polysecure is taking an ambitious step towards solving the "plastic waste" problem.
References:
1 https://www.boell.de/de/plastikatlas
2 https://www.bundesregierung.de/breg-de/aktuelles/mehr-recycling-und-weniger-verschwendung-451748