Main navigation
Bioplastics make wood cycles more sustainable
Innovative technologies and bacteria can transform wood residues into sustainable bioplastic packaging. Before bioplastics are broken down into CO2 and water in an environmentally friendly way, they can thus lead lives as products in the cosmetics industry, for example.
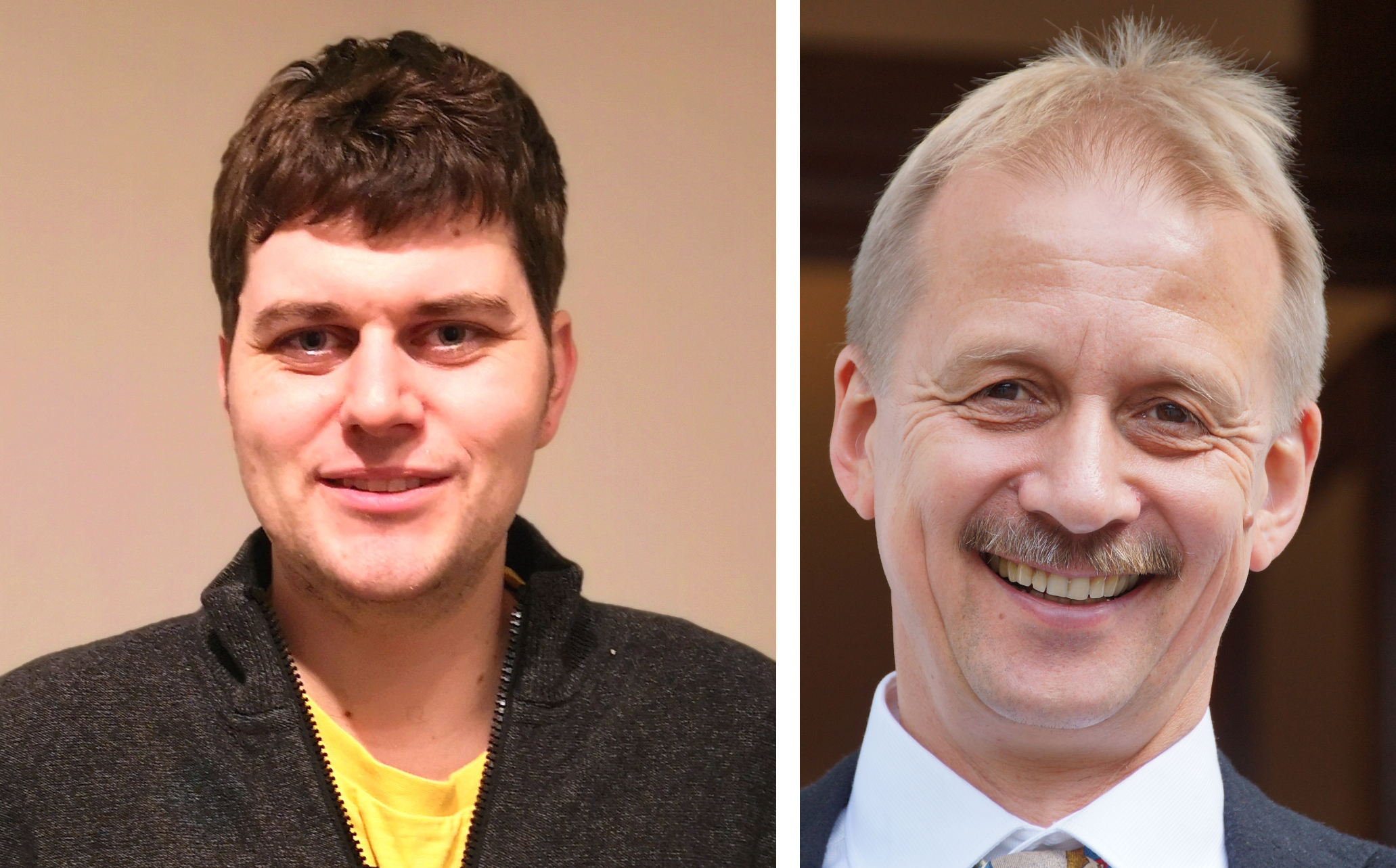
Why not use wood residues and bacteria for making bioplastics? Of course, it's not quite that simple, but it is an approach being taken by microbiologists led by Prof. Dr. Dieter Jendrossek at the University of Stuttgart’s Institute of Microbiology for the "sustainable production of polyhydroxyalkanoates for packaging materials" ("SusPackaging"). In this BMBF-funded research project, they, together with researchers from the Fraunhofer Society, are looking for an economically viable way to produce biodegradable biopolymers from wood residues. Natural cosmetics manufacturers, amongst others, are very interested in this. Associated project partners, Wala Heilmittel GmbH and WELEDA AG, are keen to use tubes and jars, shampoo bottles, soap and lotion dispensers made from sustainable bioplastic in accordance with their holistic approach. "However, we still have to clarify some basic issues before we can go into production. We have applied for funding for a second project phase in which we want to manufacture material for a test specimen, amongst other things," explains Jendrossek. This requires mechanically flexible materials that can be naturally broken down into CO2 and water after use in these and other potential applications in the food industry.
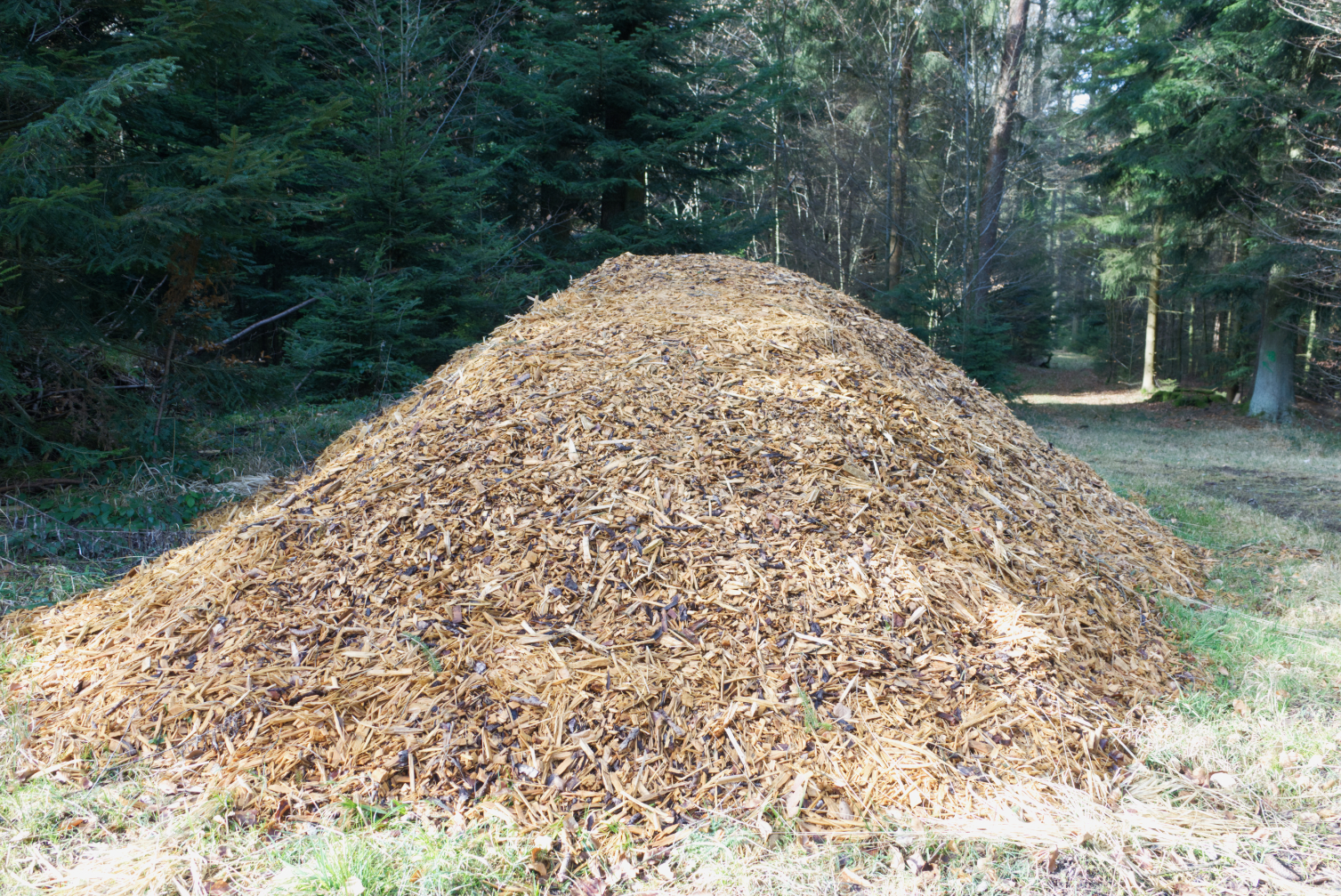
But let’s take one thing at a time. The researchers use wood residues as starting materials. These can be wood chips from a sawmill, for example. Wood residues, like all wood, primarily consist of cellulose and hemicellulose. The project partners at the Fraunhofer Institute for Interfacial Engineering and Biotechnology IGB use a chemical-enzymatic process to obtain raw glucose (from cellulose) and raw xylose (from hemicellulose). "The liquid substrates contain around 45 percent carbohydrates that bacteria can use as a source of food. However, they also contain many impurities and trace substances in an undefined composition, and this is what makes the biological process so difficult," says Dr. Felix Becker from the University of Stuttgart, who is also involved in the project. "The bacteria grow more slowly and yield less product than if they were grown on pure substrates. However, we are hoping to make a good, environmentally-friendly product from difficult substrates in an acceptable timeframe," says Jendrossek.
Micoorganisms are getting used to “dirty” substances
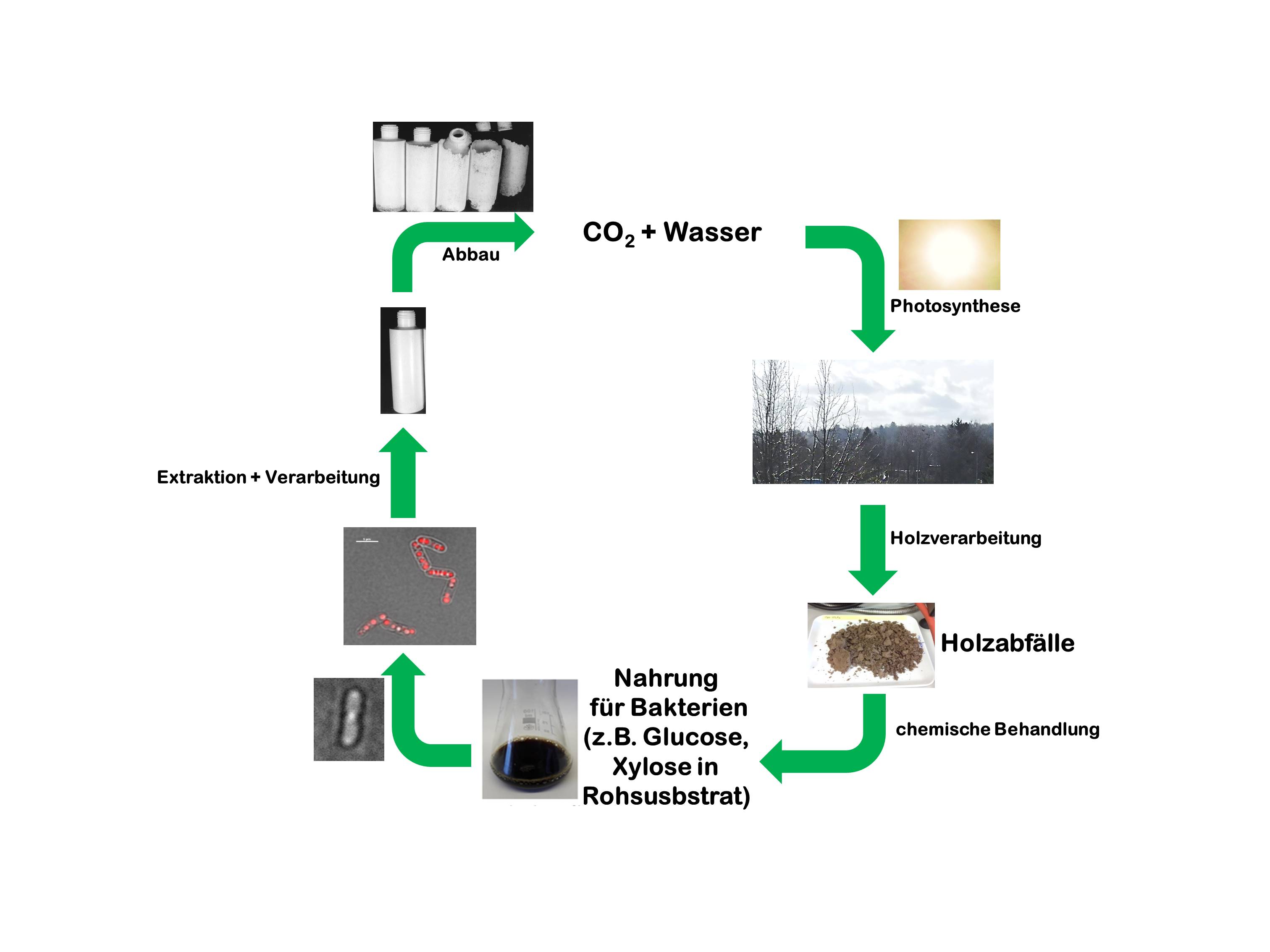
The microbiologists from Stuttgart have developed a clever strategy for this: they let evolution do the work for them. Two different bacterial species are used: the rhizobium strain Ensifer adhaerens, which was originally isolated from soil samples and tolerates impure substrates slightly better than the other strain, Paraburkholderia sacchariaus. The latter comes from a German stock collection and produces a better yield than the first. Both bacterial species slowly became accustomed to the "bad" substrate over a two-year period. This was achieved by adding ever-increasing concentrations of "bad" substrate. "We selectively multiplied the bacteria. In other words, we continued to cultivate those that, due to mutations, grew particularly well in impure medium," says Becker. The bacteria have a generation time of two to three hours, so several thousand generations can be produced within a short time. This enabled the researchers to evolve bacterial strains that can cope particularly well with impure media.
The team has now provided "proof of principle" on a laboratory scale. The next phase will be about optimising the technological process in a reactor. The focus will also be on the highest possible biopolymer yield. The biopolymers are deposited as amorphous polyester droplets in large granules in the bacterial cells. "Under optimal conditions, the bacteria consist of up to 80 percent polyhydroxyalkanoates, or PHAs for short. Our bacteria consist of around 30 to 40 percent PHAs," says Becker. In addition, there are fewer cells in total per litre of nutrient medium, simply because the bacteria do not grow as well here as bacteria grown on a pure substrate. Efficient extraction and further processing of the PHAs is therefore all the more important. A Fraunhofer team headed up by Dr. Anna Lucia Vásquez-Caicedo has developed an efficient, solvent-free extraction and purification process in the full spirit of sustainability. Production processes for PHA copolymers are now also available. The bacteria mentioned primarily produce PHAs with long-chain fatty acids, and these render bioplastics very soft. However, the mechanical properties can be controlled through combining the long-chain with shorter-chain PHAs. Derivatives of polyhydroxybutyric acid (PHB), which can also be produced biotechnologically with the help of bacteria, are suitable co-polymers.
Economic benefits depend on the general conditions
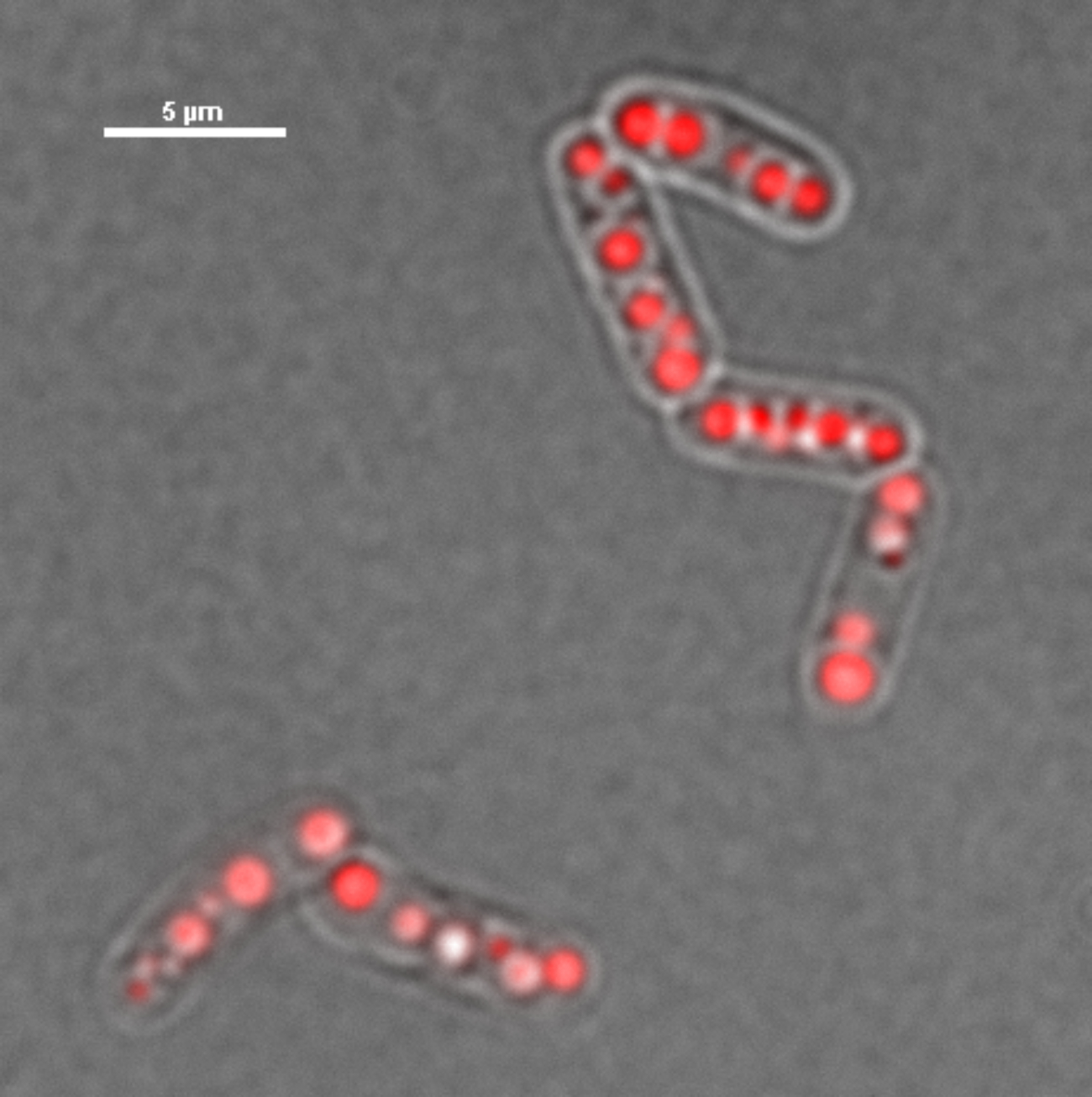
Work on upscaling bacterial production is needed to make PHA production economically interesting. According to Jendrossek, the economic viability of PHAs will ultimately rely heavily on the general conditions. "We have the opportunity to produce a good product from residues that accumulate in the forestry sector and are therefore not in competition with food cultivation. Whether this can be achieved economically is also a question of political will. It depends, for example, on how the waste materials industry develops in the future." In terms of environmentally friendly disposal, bioplastic is far superior to its petroleum-based counterpart. For example, PHA products could be shredded and composted. They could also be broken down into CO2 and water in technical reactors. The latter is faster, but may also be more expensive. Nevertheless, as the disposal of conventional plastic waste is becoming more and more complex and therefore more expensive due to environmental problems, sooner or later the time will come when bioplastics pay off simply because they can be degraded in an environmentally friendly way.
So, what about sorting? How can biobased plastics be identified and collected? Jendrossek envisages a deposit system and also believes that marking systems are worth considering. "For instance, robot systems could identify and sort bioplastics - as well as other types of plastics - relatively easily using appropriate colour coding. Technologically, marking the materials accordingly would not be a problem."