Main navigation
Straw pulp: agricultural residues become sanitary paper products
Straw cannot yet be spun into gold, but in Mannheim, Germany, it is being turned into something else of great value: Essity is the first and only company in Europe to produce toilet paper and kitchen rolls from wheat straw in a new pulp mill. From next year, these sustainable sanitary paper products will be found on supermarket shelves.
It hasn’t just been since the coronavirus pandemic that we’ve known what a major role paper plays in daily hygiene: each of us uses an average of almost 20 kg of paper per year. The proportion of recycled paper in toilet paper, household towels, paper tissues and napkins is relatively large, accounting for around 50 percent of the materials used. The other half consists of virgin wood fibres, which some German companies purchase from abroad.
Search for alternative fibres leads to the USA
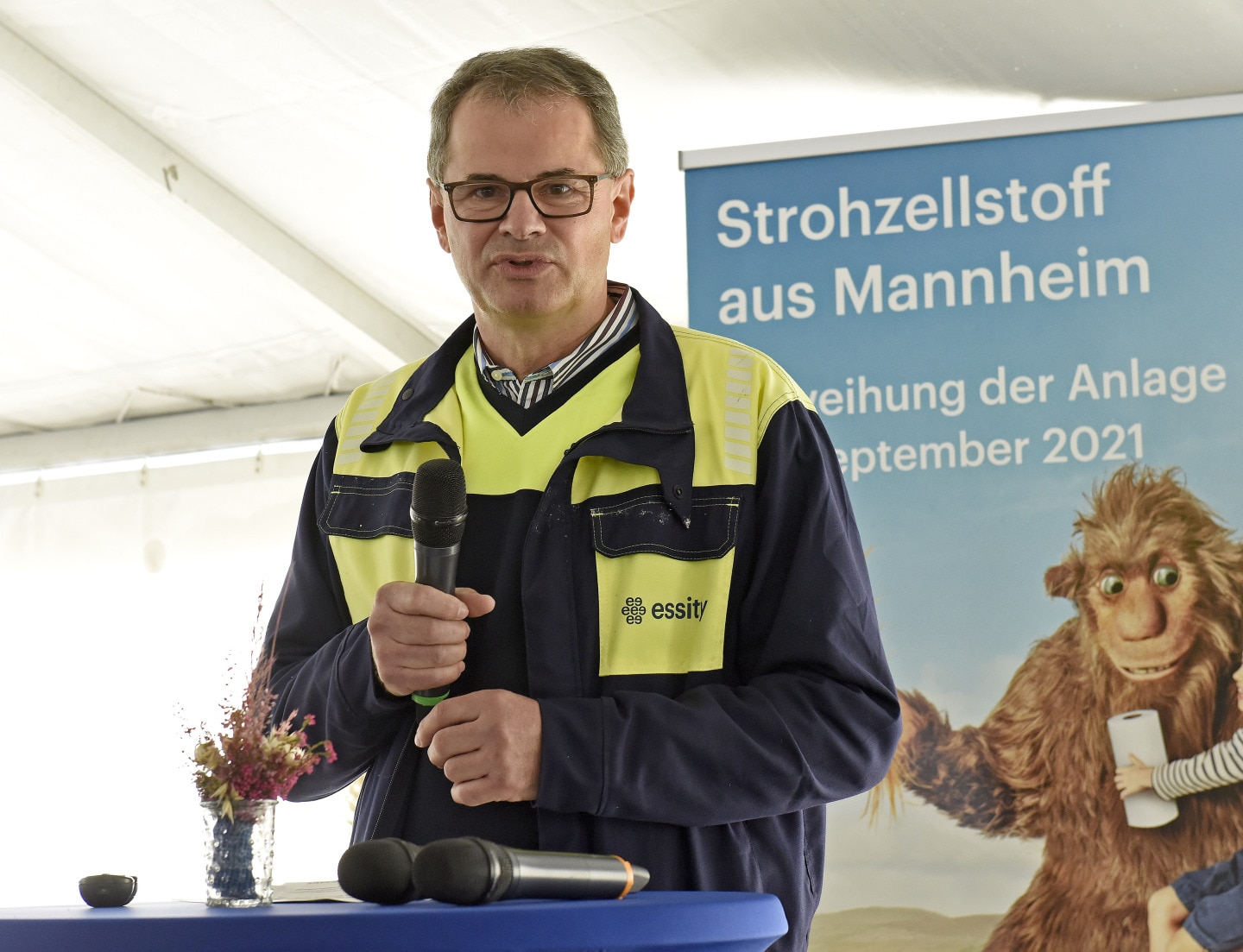
At their Mannheim company site, the Swedish hygiene and healthcare company Essity has been looking around for further options. "Essity already uses only sustainable fibres, either recycled or certified virgin wood fibres from sustainable forestry. In addition, we are constantly looking for alternatives to further improve our environmental footprint. In so doing, we came across a small American company called Sustainable Fiber Technologies SFT, which had developed a process for producing pulp from wheat straw," reports Dr. Martin Wiens, head of the straw pulp mill. "This was a completely new concept, which of course first had to be discussed in detail within our company. After all, an innovation of this kind comes with a whole lot of entrepreneurial risk attached. However, we are absolutely convinced by the new process and have therefore signed a license that secures us the exclusive rights of use for Europe - a major advantage over our competitors." Another plus of the process is that it requires less water and energy than conventional pulp production.
Since then, a lot of planning, building, tinkering and development has been going on at Essity's largest European production site in Mannheim. Founded way back in 1884 as Zellstofffabrik Waldhof, the traditional company can draw on a wealth of experience in pulp production. Currently, 283,000 t of pulp are produced in Mannheim from certified virgin wood fibres and wood residues and processed into tissues, household and paper towels as well as toilet paper and napkins. Since October 2021, an additional 35,000 t of straw pulp have also been added.
Novel pulp from wheat straw as a third mainstay
In the new 'mill within a mill', which represents a 40- million-euro investment for Essity, around 70,000 t of wheat straw are processed into a new type of pulp on an area of 8,000 m2. This new type of pulp is said to be just as soft, tear-resistant and absorbent as conventional products. "This completely new fibre source is a third mainstay, alongside classic tissue and recycled paper. It gives us a lot of flexibility," Wiens explains. "From the outset, our key stipulation was that customers should not notice any qualitative difference between conventional tissue paper and the paper with straw content."
The raw material for the new type of eco-paper comes from local farmers : "Straw is a residual product left over after the grain harvest. Only the wheat grain is used to produce food, and a large amount of straw remains unused," says the expert. "By using these residues, we can reduce the amount of wood-based pulp we purchase from abroad, transport distances are shorter and CO2 emissions can be reduced. Overall, pulp made from straw has at least a 20 percent smaller environmental footprint than pulp made from wood or recycled fibres."
Grain waste is turned into the kind of tissue paper products we are used to
Another plus point is that the straw bales Essity uses represent a new, reliable source of income for farmers. After the grain harvest, the stalks are cut between the ear and the ground residue and pressed into bales. "However, it was not that easy to get hold of large quantities of straw at first, as there is no real straw market here in Germany yet," says Wiens. "The straw is only traded on a limited basis locally. Purchasing networks don't yet exist and have to be established first. An external company does this for us and organises the purchasing. Our daily supply has to be ensured, because straw is only harvested once a year, but has to be available to us all year round."
Therefore, the new plant also incorporates a 10,000 m2 straw storage area, from where the heavy bales are transported directly to pulp production via a conveyor belt. "Here, a fast turnaround takes place. The bales are stored for a maximum of five days. So it doesn't matter if they are exposed to rain during storage," Wiens reports. On the conveyor belt, the bales are dewired, cleaned of dirt and sorted. To turn straw into pulp, the straw is first boiled to extract the pulp fibres from it. Then, in another step, the fibres are lightened. "You could certainly leave the typical yellowish hue of straw as it is, but customers are used to white sanitary paper products, so we're sticking with that for now," Wiens says. "Bleaching is completely chlorine-free. We use peroxide similar to that used for dyeing hair."
The white pulp is then cleaned. This process takes place in an historical building that was formerly used as a spare parts store and has now been converted into a new factory hall. Afterwards, the finished pulp is temporarily stored in the pulp storage tower and can be pumped in liquid form directly to the paper machines via the supply line that is over 1 km long.
The packaging is also created at the same time
Lignin is one of the by-products of this process. This valuable biopolymer is not disposed of with the waste, of course, but is concentrated and will later be supplied to other branches of industry as a raw material. For example, it can be used as a tanning agent for leather goods or as a binding agent for animal feed and building materials. In addition, it can be admixed to produce a yellowish plastic film. "One idea is to use this film as packaging for our sanitary paper at some point in the future," says the straw factory manager. "Although this won’t be happening tomorrow, initial tests show it would be possible."
The novel products were widely accepted by test consumers: "Of course, we don't undertake such a huge project without carrying out a consumer survey first," Wiens reports. "The response to the products from our test facility has been extremely good, especially in terms of the story we have to tell: from waste material to grain production to an everyday product."
Using additional renewable sources in the future
The novel sanitary paper products are to be launched on the market in 2022. The marketing strategy is currently being developed. At the same time, the straw pulp mill has started operating.
"In principle, the process can be adapted to all annual crops", says Wiens. “We have started with wheat straw because around 11 million tonnes are available per year in Germany, which is the largest quantity of all grain straws. In the future, however, we’ll also be able to incorporate other types of grain."