Main navigation
Using fungi to create sustainable and economical mycelium-based materials
Most of us see fungi as just food - and possibly pathogens. This is a mistake, because these amazing organisms are capable of much more: they grow on plant residues of all kinds, forming a dense and interconnected structure as they spread. The resulting material can be moulded into desired shapes and be turned into new sustainable and economically attractive products such as leather and polystyrene substitutes or building materials. The manufacturing process for these mycelium materials has been established, and companies are now needed as pioneers to turn this innovation into reality.
Fungi are neither animals nor plants, despite being long thought the latter. They rather form their own kingdom of life, and are organisms that extend beyond the fruiting body that we see. The vegetative body of fungi runs underneath the ground, where it forms a widely branched network of wafer-thin fungal threads, very similar to plant roots. This so-called mycelium can reach almost unimaginable dimensions: one square metre of soil can easily contain a billion fungus mycelia. It is an extremely efficient system that is not at all demanding, grows through organic material of all kinds and binds the mixture into a solid mass.
Fungal spore plus residual material produces innovative material in many and varied forms
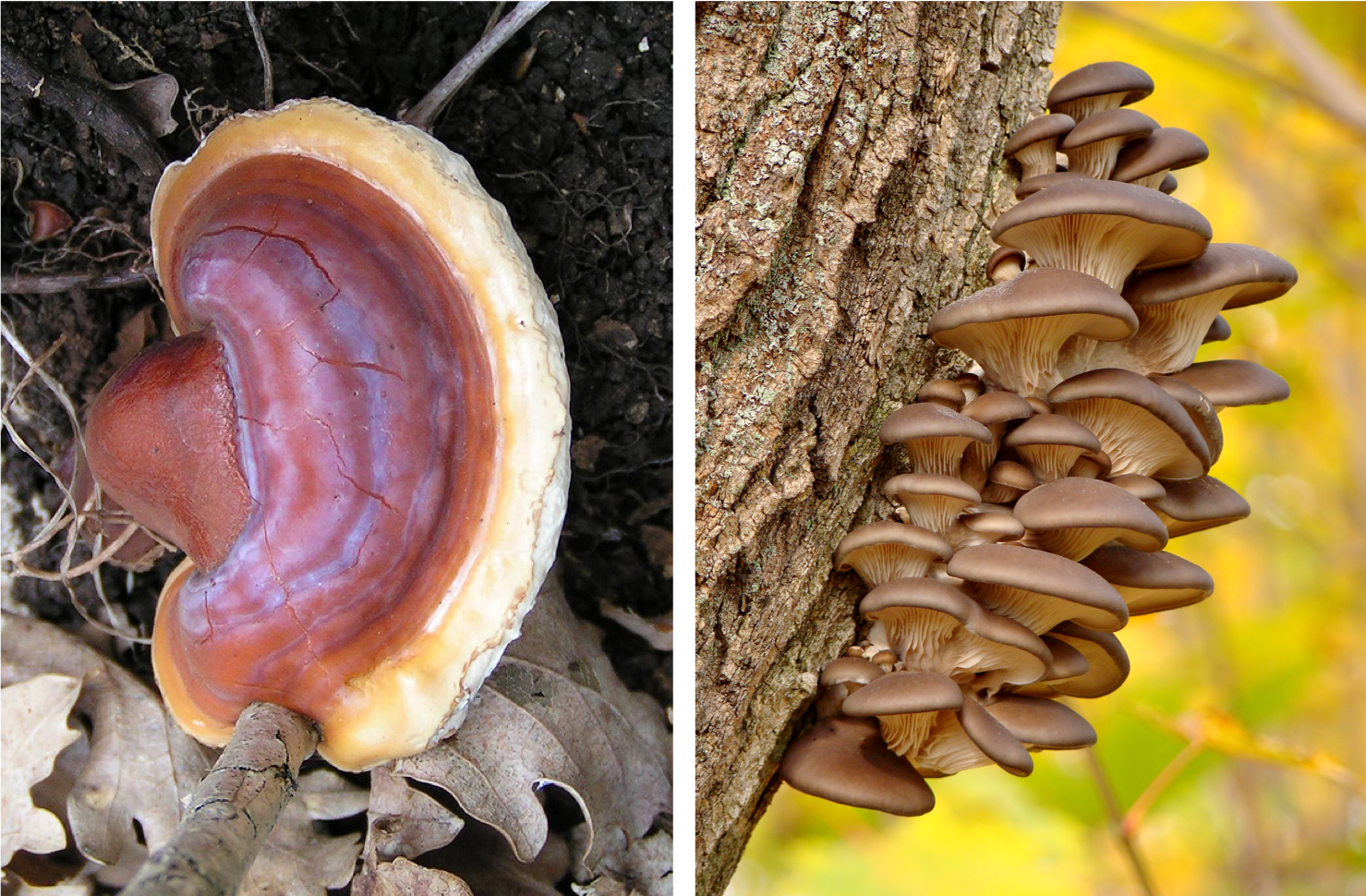
Mycelium is therefore an interesting candidate for producing new, sustainable materials. Researchers discovered this potential many years ago and began experimenting with mycelium-based materials. The experimentation proved a success, and led to a well-established manufacturing process for a wide variety of materials. The method is simple: fungal spores are added to waste materials such as sawdust or shredded plant stems that would otherwise be incinerated, or even organic waste such as coffee grounds. The possibilities are almost limitless, as most types of fungi are extremely frugal, growing on and penetrating almost any organic substrate. The type of waste material determines, among other things, the desired application, i.e. the subsequent material properties and quality. In other words, whether the desired product will be soft and flexible or hard and robust. Product hard- or softness can also be influenced through the combination of mycelium with materials such as limestone or by directly affecting the density of mycelium growth.
But that's not all: there are currently over 100,000 recorded species of fungi (although it is estimated that there are up to 4 million).1) Depending on the species chosen, this can lead to an infinite number of possibilities for producing different materials. Once grown into a mould, the solid pieces are then dried to stop growth and pressed into mouldable materials. An alternative option is to produce a paste for 3D printing from the residual materials and subsequently allow the fungus to grow through.
Houses, furniture, packaging, composites and much more
The actual products that have already been made from mycelium-based materials are astonishing: anyone who only associates mushroom houses with dwellings for gnomes needs to think again. A team from the Karlsruhe Institute of Technology (KIT) has used the Ganoderma lucidum tree fungus and wood chips in combination with hemp or flax fibres to produce building blocks for house construction and this could possibly be used to grow entire walls. A house made in this way could then simply be disposed of in the compost. It may also be possible to produce a mycelium-based substitute for climate-damaging concrete. The potential of the biobased and biodegradable material for the construction industry is therefore extremely high due to its special properties such as good fire resistance, heat and sound insulation, low density and weight as well as the possibility of processing it into end products of a variety of shapes.
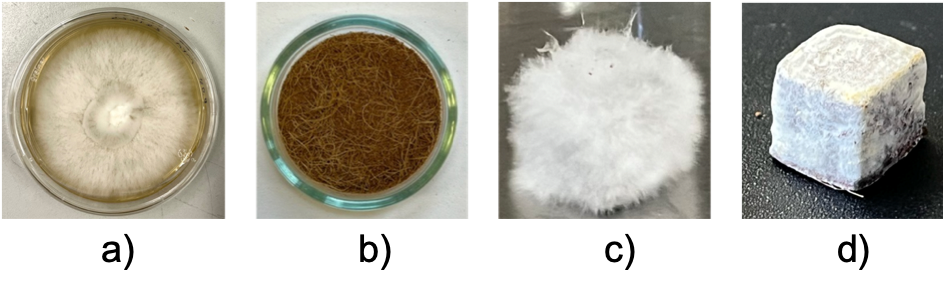
Other pioneers in the development of mycelium-based products include researchers at Fraunhofer Institutes: the Fraunhofer Institute for Applied Polymer Research IAP in Potsdam, for example, is working on animal-free alternatives to leather products to make vegan shoes, purses, furniture and interior fittings for cars, among other things. Their potential for packaging is also being researched. Solutions in this area are already being successfully marketed in the USA, for example as a substitute for polystyrene, and are being used by high-profile customers such as Dell and Ikea. Sustainable alternatives to plastic are in huge demand in all kinds of areas, and mycelium-based products are therefore extremely promising for companies that produce them.
Fraunhofer researchers are also already focusing on the further optimisation of material performance, quality assurance for specific applications and suitable industrial manufacturing processes. On a platform called the LoopOfFun (Closed-loop control of fungal materials), for example, various international partners are working on the rapid development of industrial, single-stage, simple casting manufacturing processes for multi-structural materials based on renewable and locally sourced raw materials.
There is so much more that can be added to the list of new products and ideas from nature’s workshop: the Fraunhofer Institute for Environmental, Safety and Energy Technology UMSICHT in Oberhausen has developed a 3D-printed sound absorber made of fungus-based materials, while the Fraunhofer Institute for Building Physics IBP in Stuttgart has developed other insulating materials. The researchers have already demonstrated that their thermal insulation can compete with commercially available eco-friendly insulation materials.2)
There are many ideas for products made from fungal mycelia in other sectors. These range from food as a meat substitute to circuit boards for electronic components, organic wound dressing material, robot skin that heals itself and much more.
The materials are economically viable and sustainable
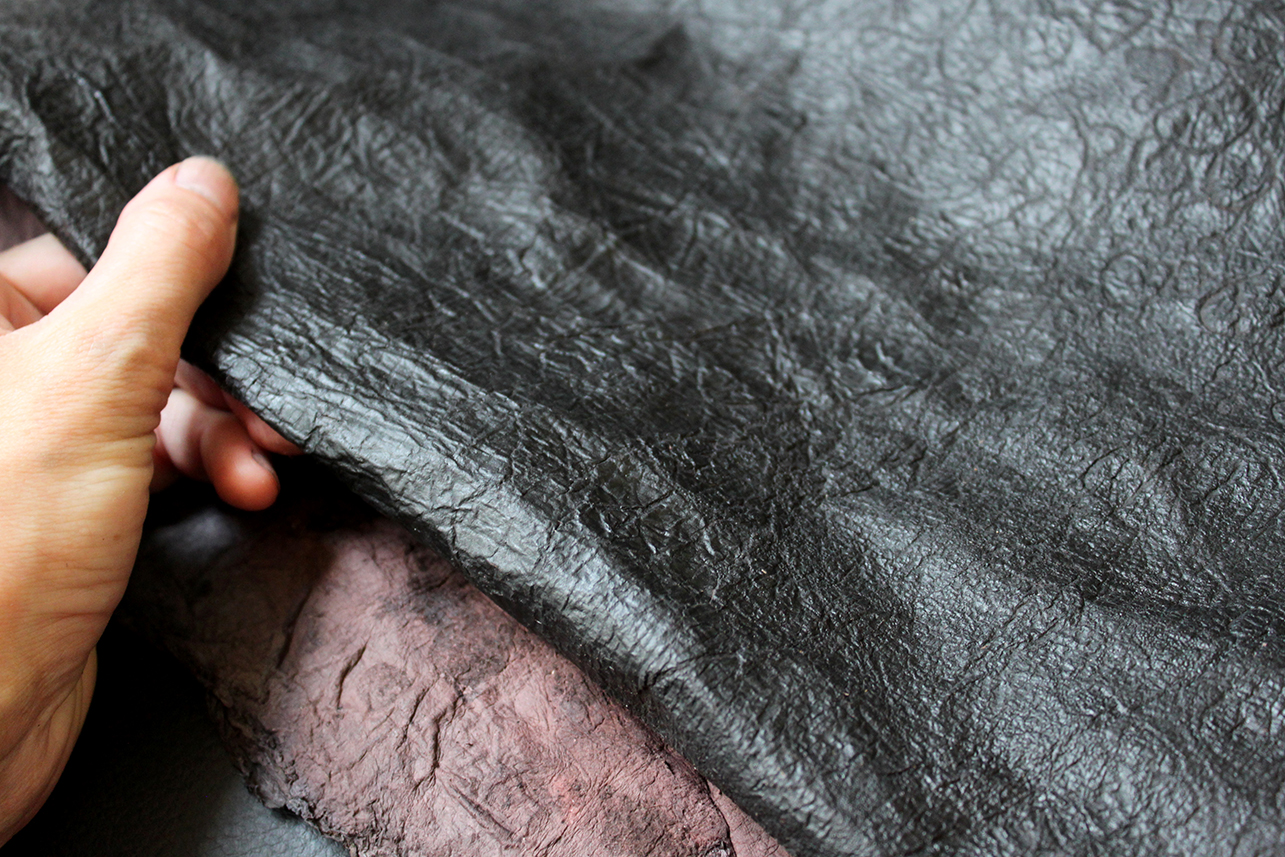
The future potential of mycelium-based materials is therefore huge - provided we don't miss the boat. "Both the production costs and the ecological footprint are much more favourable than that of current fossil-based materials," explains Sabine Krieg, Innovation Manager at the Fraunhofer Institute for Interfacial Engineering and Biotechnology IGB in Stuttgart. "This is because far less energy is needed to produce them and, thanks to their natural origin, fungus-basedmaterials save resources and are biodegradable."
Together with Dr. Liliya Pullman from the Fraunhofer Institute for Systems and Innovation Research ISI in Karlsruhe, Krieg is working on reconciling economic and environmental goals in industry and society, and one of the areas she is looking at is sustainable material made from mycelium: "On the production side, the materials can be processed on standard machines without requiring wholescale adaptation. This has already been tested at the VTT Finland research institute, which successfully produces mycelium leather in a roll-to-roll process - so you don't have to reinvent manufacturing and can quickly become economically viable." Pullmann adds: "We believe the potential of the material is so great, because it is economically interesting and saves resources - making it an extremely attractive new field, especially for Baden-Württemberg. A transformation is imminent and would be of interest to the construction and packaging industries as well as the automotive sector and its suppliers, for example. There are plenty of ideas."
So not only the raw materials themselves are sustainable, but also the way they are produced: "Waste streams are generated locally," says Pullmann. "It does not occupy land used for agriculture or the transport of raw materials over long distances. This means that entire supply chains can be organised optimally, sustainably and locally. And this protects existing jobs by adaptation through further training as well as creating new ones."
Funding programme for material innovations on the wish list
However, quick action is needed, as international competitors have also recognised the (economic) potential. "Now it's up to business promoters to bring together residual materials, mycelium-based materials and companies across all sectors - materials seeking application and vice versa," says Krieg. "If we get involved now, Baden-Württemberg could soon become an international innovative materials top-location as well as one of the automotive industry. Internationally, there is already a growing community of start-ups that are literally springing up like mushrooms. Now we also need to develop prototypes, carry out acceptance, demand and incentive studies and advise companies. Fortunately, this is an area that is increasingly being mentioned in publicly funded projects, but far too little is being done about it. One of the things we would jointly ask the Ministry of Economic Affairs, Labour and Tourism Baden-Württemberg would be to implement a funding programme for material innovations. This would be a real accelerator that would benefit companies in the state. Because with materials 'made in Baden-Württemberg', we could really score competitively."
References:
1) Freie Universität Berlin, press release (2017): "Pilze sind das zweitgrößte Organismenreich der Erde: Studie schätzt globale Pilzvielfalt auf 2,2 bis 3,8 Millionen Arten.“ www.bgbm.org/de/pr/pilze-sind-das-zweitgroesste-organismenreich-der-erde-studie-schaetzt-globale-pilzvielfalt-auf
2) E. Kotan et al. (2023): "Bauphysikalische Untersuchungen an Myzel-basierten Materialien für den Einsatz als Wärmedämmmaterial“. Bauphysik 45 (1), 55 – 59. https://doi.org/10-1002/bapi.202200040