Main navigation
Novel fibre composite made from hop fermentation residues
Biogas plants produce energy-rich gas by fermenting biomass. This process generates both liquid and solid fibrous and particulate fermentation residues. Researchers at the German Institutes of Textile and Fibre Research (DITF) have now managed to create a resistant and water-repellent fibre composite material from solid hop residues that can be used as a veneer to coat wood panels.
Germany is one of the world's leading consumers of beer, and German beer brands are hugely popular internationally. The world's largest continuous hop-growing area, the Hallertau, is located between the cities of Regensburg, Ingolstadt and Landshut. Around 85 percent of the hops processed in Germany are grown here. However, only the hop umbels are used for the brewing process; three-quarters of the plant is biowaste and, after harvesting in autumn, is shredded and either fed into a biogas plant or returned to the fields. However, returning them to the fields is not particularly effective as the plant residues are often not sufficiently decomposed by the following spring to be good fertiliser for the new vines. Additional fertiliser needs to be applied.
Nonwoven fabric from hop fermentation residues
However, biogas plants can extract gas (mainly methane and CO2) from organic waste with the help of bacteria and in the absence of oxygen. This gas is then either fed directly into the natural gas grid or used to generate electricity and heat in a combined heat and power plant. The remaining fermentation residues also contain nutrient-rich liquid fertiliser in addition to fibrous material that is difficult to break down. "Electricity from biogas plants is significantly more expensive than electricity generated by onshore wind power. To increase the economic viability of the plants and create added value, we investigated whether the solid residues from hop fermentation could be used, for example, to produce fibre composites," explains Prof. Dr. Markus Milwich, deputy head of the Polymers & Fibre Composites Competence Centre at the German Institutes of Textile and Fibre Research (DITF) in Denkendorf and honorary professor at Reutlingen University of Applied Sciences.
Under his supervision, doctoral student Marion Gebhardt has been working on this issue for the past two years as part of a research project funded by the Central Innovation Programme for SMEs (ZIM). "In a first step, we tried to produce a nonwoven fabric from the washed, fibrous residues," explains the agricultural engineer. "To do this, we tested a wide variety of methods and screened, shredded or ground the material. At some point, we came across the Hollander beater." This machine was used in pre-industrial papermaking from the 18th century onwards and is still used today. It consists of a roller with cutting edges that finely pulverises the material without over-shortening the fibres.
Water-repellent fibre composite material for coating
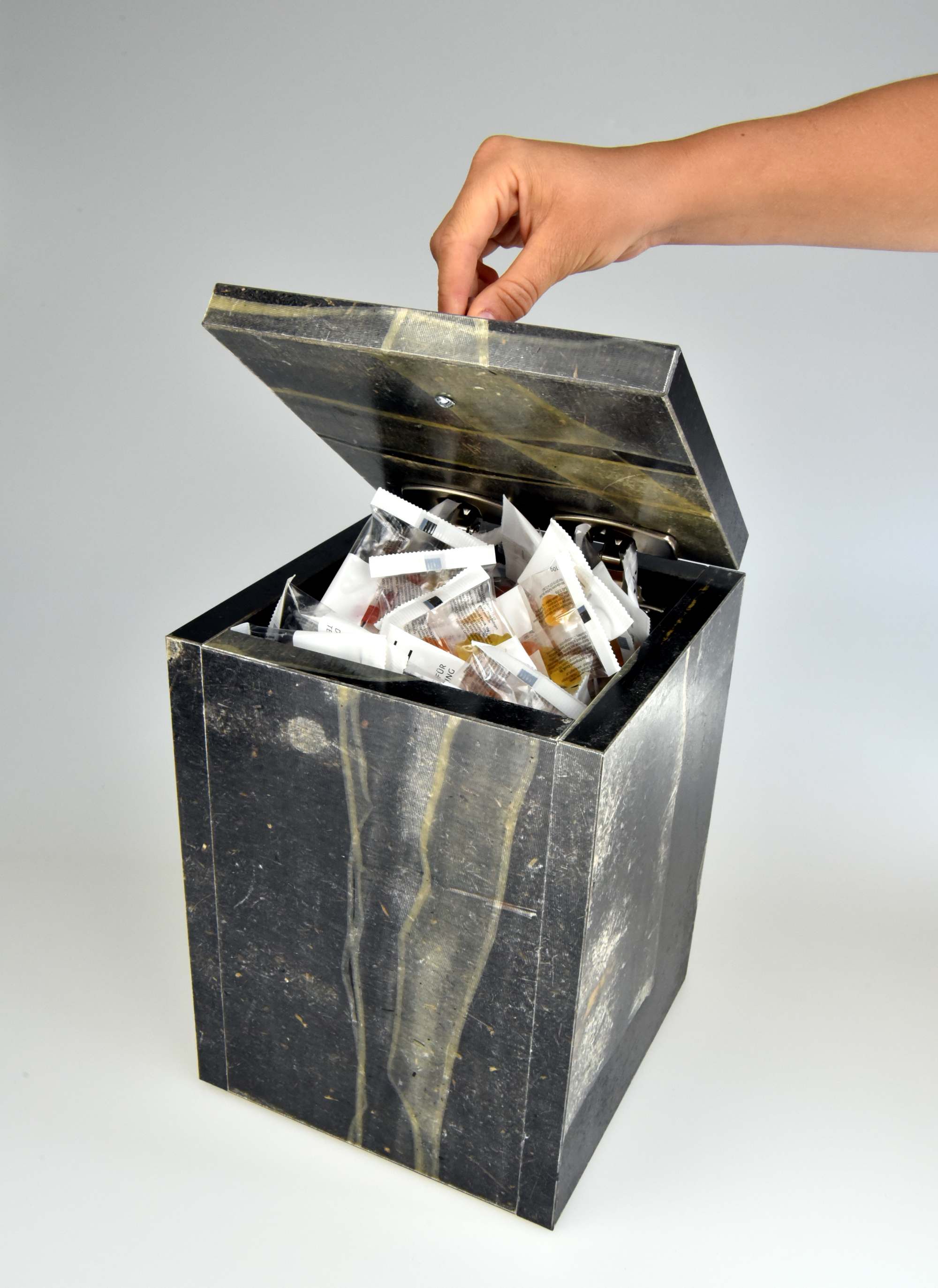
In cooperation with Reutlingen University of Applied Sciences, mats are produced in a wet nonwoven plant from solid fermentation residues that have been treated in this way. The correct ratio of fibres, water and pulp first had to be determined to ensure that the nonwoven mats were stable but not too firm for further processing. In the next step, the mats are pressed in a hot press at up to 6 megapascals (MPa) together with an epoxy resin to form a fibre composite. "We use only biobased resins, which require a temperature of around 100 °C to cure quickly," says Gebhardt, describing the procedure. This makes it possible to produce panels less than 1 mm thick, which can be used as veneers to coat wood fibreboard. The problem-free processing of the composite material has already been demonstrated as part of the project by the Nuding carpentry in Stuttgart, which has used it to produce its first furniture components. A major advantage of the material is its water-repellent property, which could make painting the pieces superfluous.
This new type of fibre composite material has the same stability as MDF (medium-density fibreboard) panels. However, it weighs more, meaning that boards 15 to 18 mm thick as required for furniture are relatively heavy. Another problem can be the material’s dark brown colour; but this can be changed to some extent by adding biological bleaching agents and colour pigments.
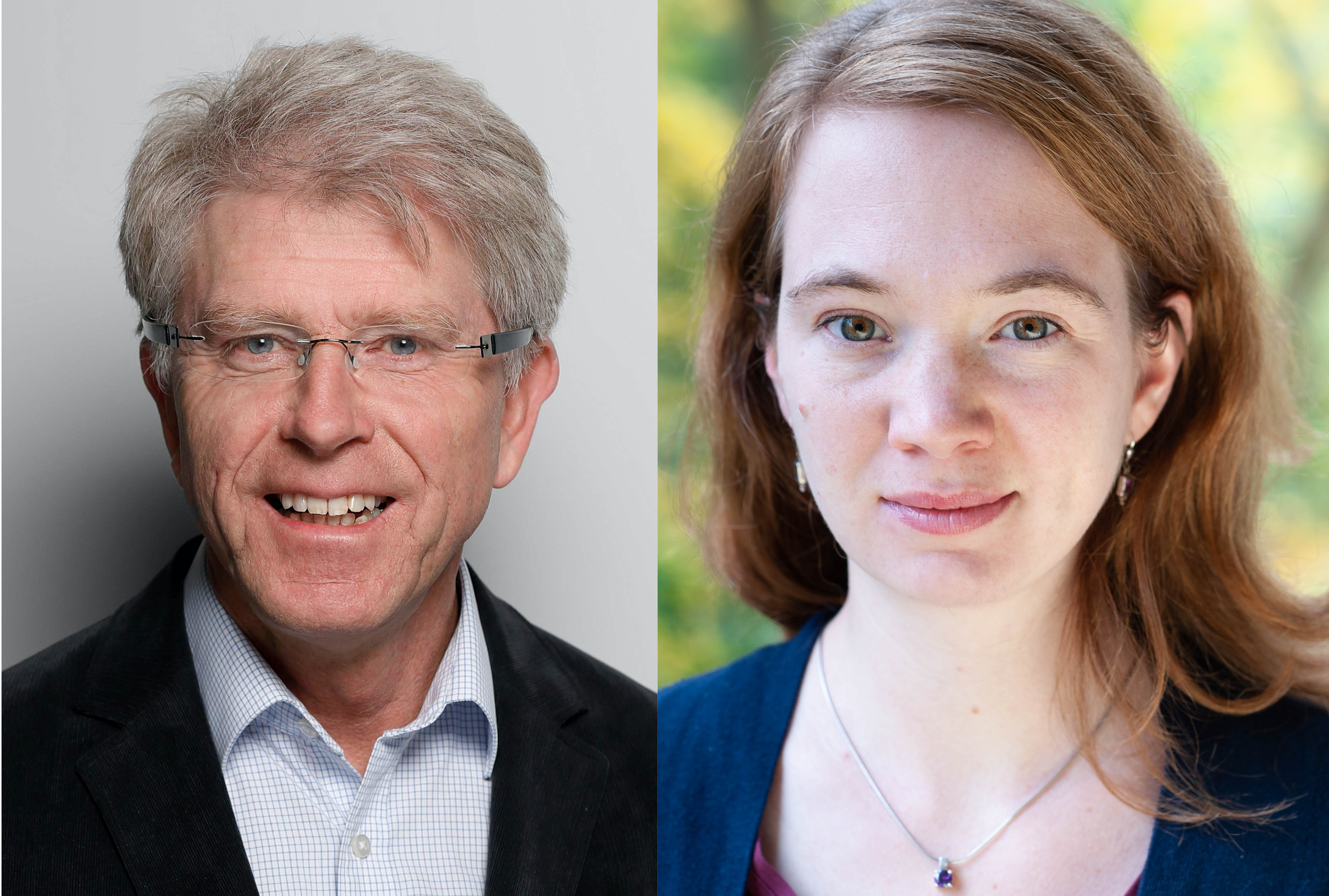
Milwich, together with his project partners, Hopfenpower GmbH (specialists in the comprehensive recycling of hops) and Novis GmbH (manufacturer of biogas plants), is currently looking for other companies to test and further develop products based on the new composite. For him, conceivable projects would include cooperating with breweries to test coated beer benches. Both the dark colour and the water-repellent properties are well suited for coated beer benches. "We expect that the beer benches coated with our fibre composite will last longer. Another advantage would be that at the end of their lifetime, they do not have to be disposed of as expensive special waste [like furniture painted with wood preservatives]," says the engineer. It would also be possible to use the composite material in the automotive industry as interior panelling for vehicles, because the material can be pressed into any shape.
Full use of plant residues
Initial investigations show that it’s not just hops that are suitable as a starting material for producing composites, but also hemp or straw, for example. Milwich also sees huge potential in water hyacinths, a plant species native to South America that is now spreading weed-like in warm regions around the world. "Normally, plant fibre digestion is done by steam explosion and other methods, which is relatively costly. In a biogas plant, this work is done by bacteria." In Africa, for example, where Novis GmbH is already operating, the new process would allow water hyacinths to be fully utilised for producing electricity and fertiliser, and as a feedstock for manufacturing construction materials.